tpo membrane
TPO Membrane Introduction
TPO (Thermoplastic Polyolefin) waterproofing membrane is a lightweight, flexible, and energy-efficient roofing solution. Renowned for UV resistance, chemical durability, and heat-reflective properties, it offers seamless installation via heat welded seams, ideal for commercial roofs, green buildings, and industrial structures while meeting eco-friendly standards.
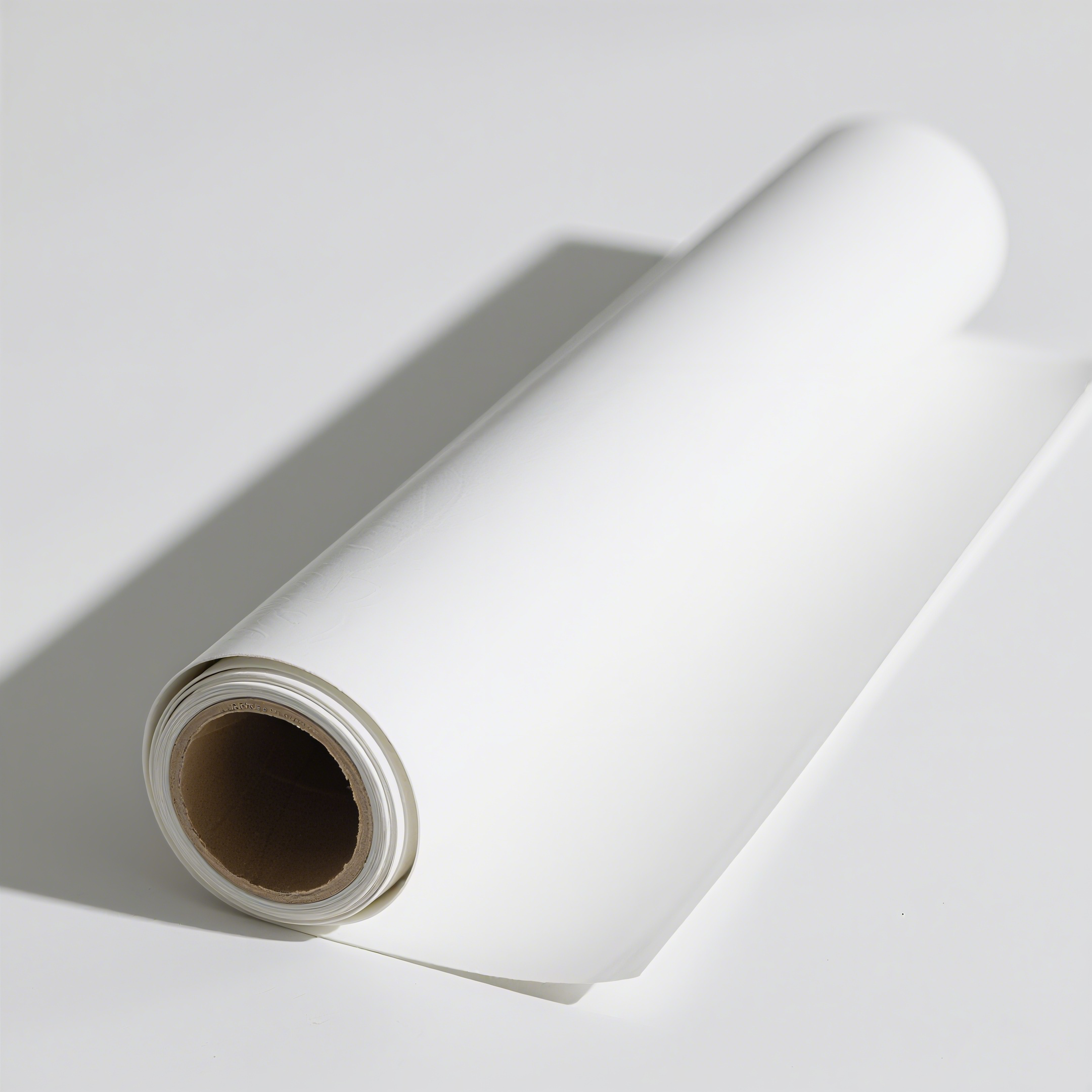
TPO Membrane Specification
Thickness | 1.2mm, 1.5mm,1.8mm, 2mm, or customized | ||
Roll width | 1m, 2m, or customized | ||
Roll length | 15m/roll,20m/roll, 25m/roll or customized. | ||
If exposed | Exposed or Non-exposed. | ||
Color | white, gray, or customized. | ||
Standards | ASTM/GB |
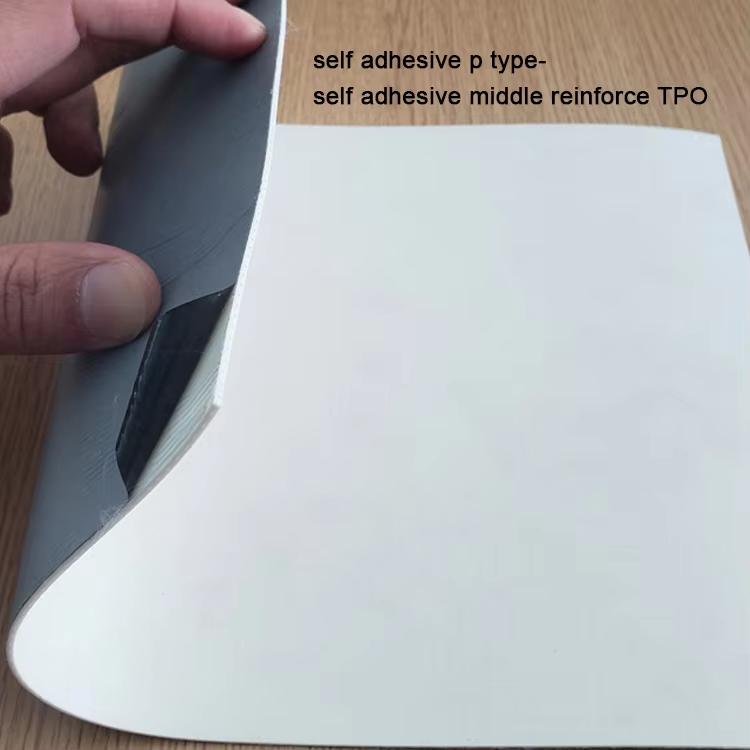
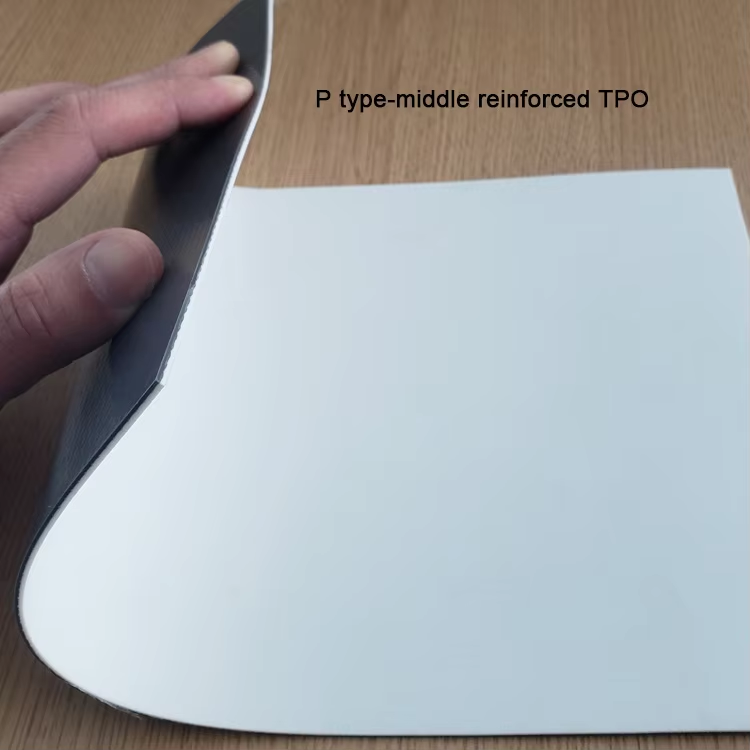
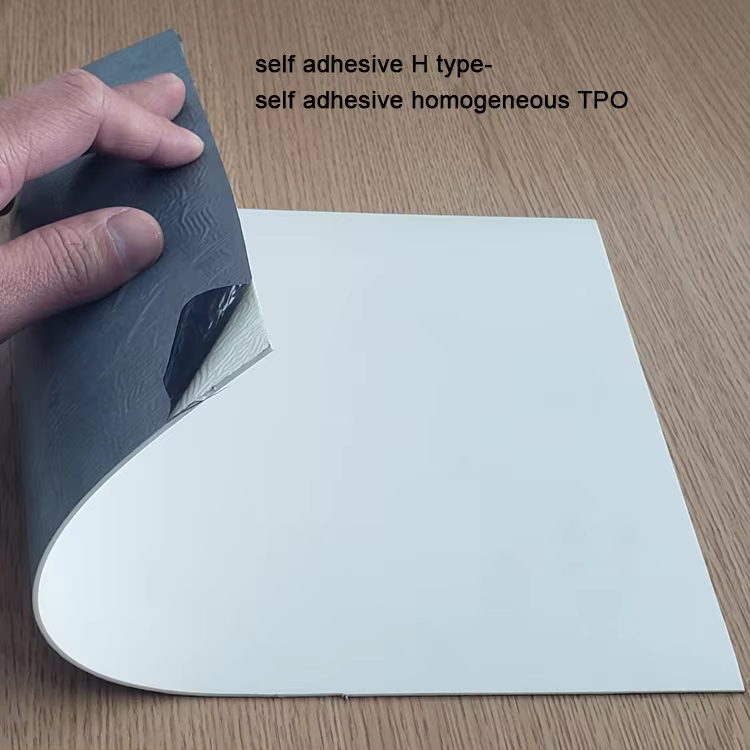
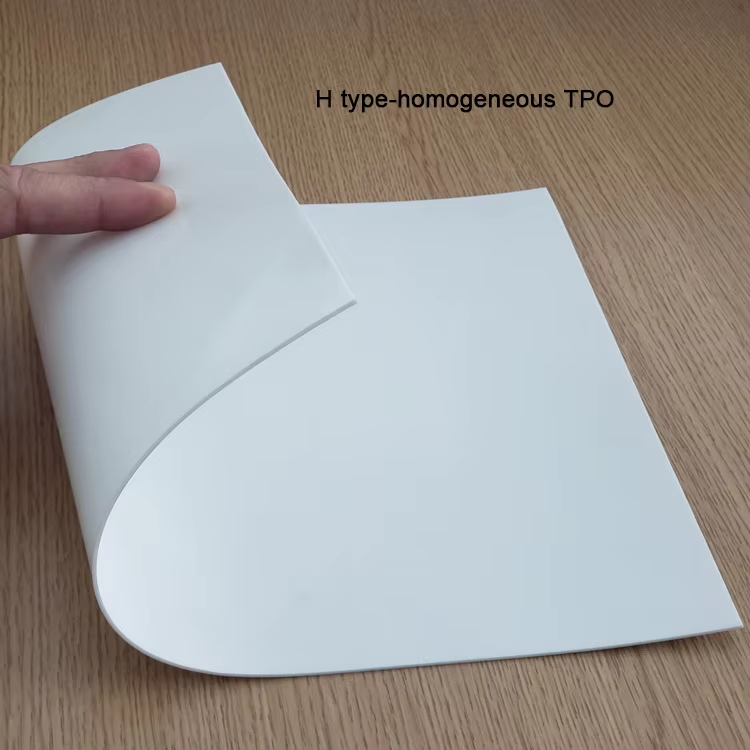
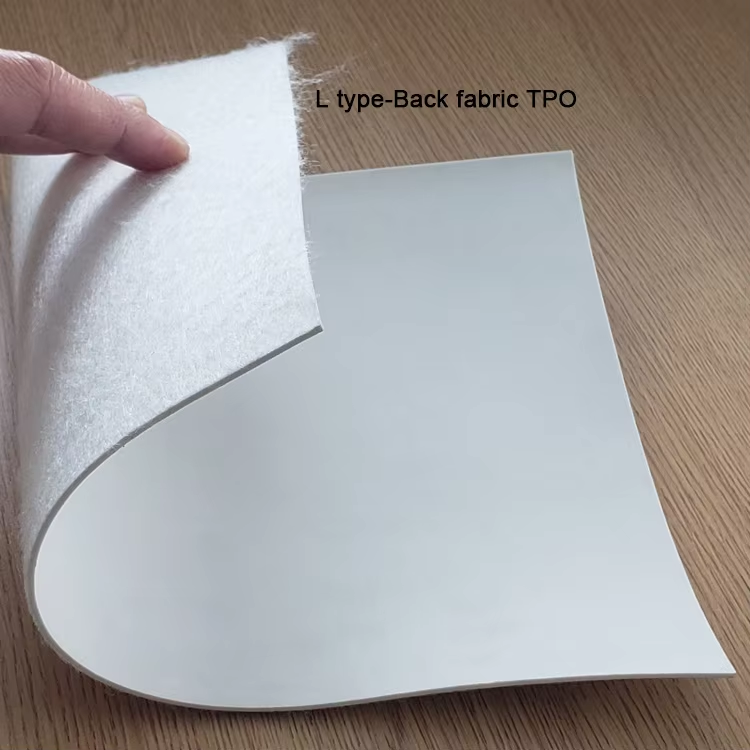
TPO Mrmbarne Standard
No. |
Item |
Standard |
|||
H |
L |
P |
|||
1 |
Thickness of material on the reinforcement/mm ≥ |
- |
- |
0.40 |
|
2 |
Tensile Property |
Max Tension/ (N/cm) ≥ |
- |
200 |
250 |
Tensile Strength/ Mpa ≥ |
12.0 |
- |
- |
||
Elongation Rate/ % ≥ |
- |
- |
15 |
||
Elongation Rate at Breaking/ % ≥ |
500 |
250 |
- |
||
3 |
Heat treatment dimensional change rate |
2.0 |
1.0 |
0.5 |
|
4 |
Flexibility at low temperature |
-40℃, No Cracking |
|||
5 |
Unpermeability |
0.3Mpa, 2h, No permeability |
|||
6 |
Anti-impact property |
0.5kg.m, No seepage |
|||
7 |
Anti-static load |
- |
- |
20kg, No seepage |
|
8 |
Peel Strength at joint /(N/mm) ≥ |
4.0 |
3.0 |
3.0 |
|
9 |
Right-angle tear strength /(N/mm) ≥ |
60 |
- |
- |
|
10 |
Trapeaoidal tear strength /N ≥ |
- |
250 |
450 |
|
11 |
Water absorption rate(70℃, 168h) /% ≤ |
4.0 |
|||
12 |
Thermal ageing (115℃) |
Time/h |
672 |
||
Appearance |
No bundles, cracks,delaminatetion,adhesion or holes |
||||
Performance retention rate/ % ≥ |
90 |
||||
13 |
Chemical Resistance |
Appearance |
No bundles, cracks,delaminatetion,adhesion or holes |
||
Performance retention rate/ % ≥ |
90 |
||||
12 |
Artificial climate accelerates ageing |
Time/h |
1500 |
||
Appearance |
No bundles, cracks,delaminatetion,adhesion or holes |
||||
Performance retention rate/ % ≥ |
90 |
||||
Note: | |||||
1. H type is the Normal TPO membrane | |||||
2. L type is the Normal TPO coated with the non-woven fabrics at the back side | |||||
3. P type is the Normal TPO reinforced with the fabric mesh |
Product Features
1. It has anti-aging, high tensile strength and high elongation;
2. It has excellent weather resistance and low-temperature flexibility. The overlap seams are constructed by heat welding to form a high-strength reliable sealing waterproof layer;
3. It has good processing performance and mechanical properties;
4. It can be constructed on wet roofs, exposed without protective layer, easy to construct, pollution-free, and very suitable as a waterproof layer for light energy-saving roofs;
5. The enhanced TPO waterproof membrane has a layer of polyester fiber fabric in the middle, which is more suitable for mechanically fixed roof systems. After adding a layer of polyester fiber fabric between two layers of TPO material, its physical properties, breaking strength, fatigue resistance and puncture resistance can be enhanced.
6. Backing type TPO waterproofing membrane, the fabric on the lower surface of the membrane makes the membrane easier to bond with the base layer.
7. Homogeneous TPO waterproofing membrane has good plasticity and can be processed into various shapes after heating to adapt to the practice of complex nodes.
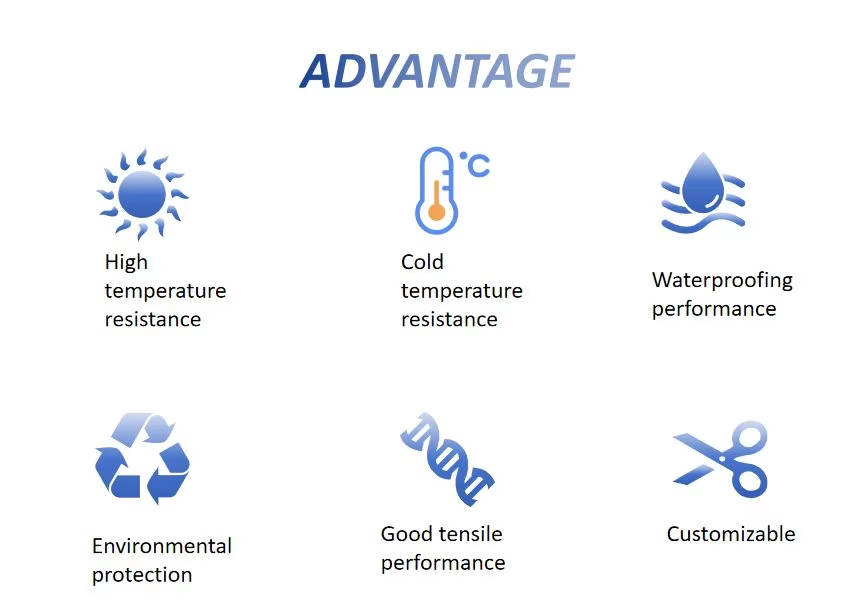
TPO Membrane Application
1. It can be applied to the exposed or non-exposed roof waterproofing layer of buildings, and the underground waterproofing of buildings that are easy to deform;
2. It is especially suitable for light steel structure roofs, and is the preferred waterproof material for roofs of large industrial plants, public buildings, etc.;
3. It can also be applied to waterproof and moisture-proof projects such as drinking water reservoirs, toilets, basements, tunnels, grain depots, subways, reservoirs, etc.
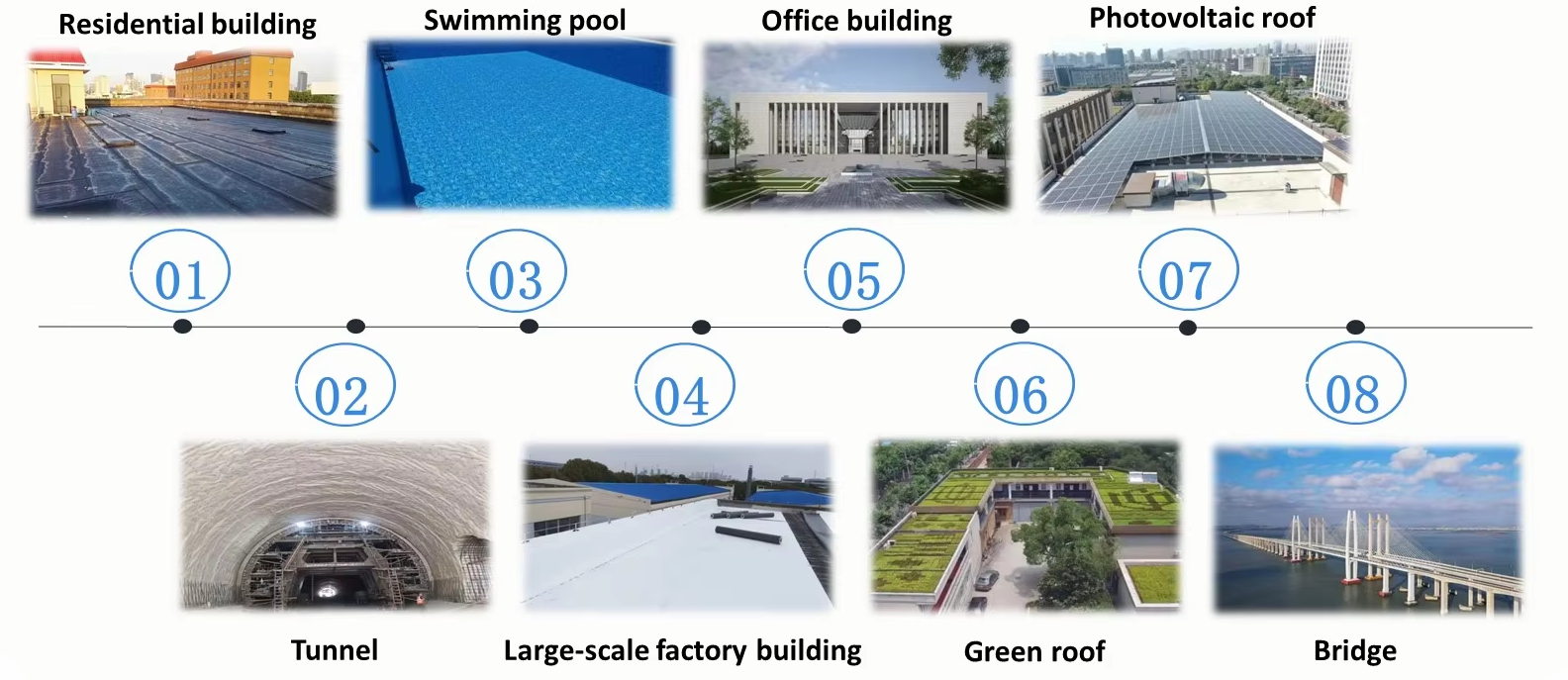
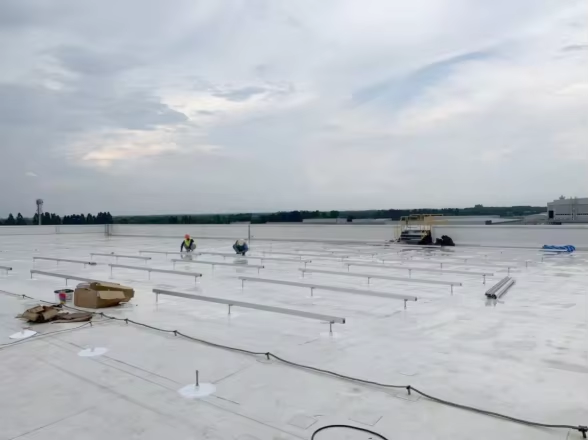
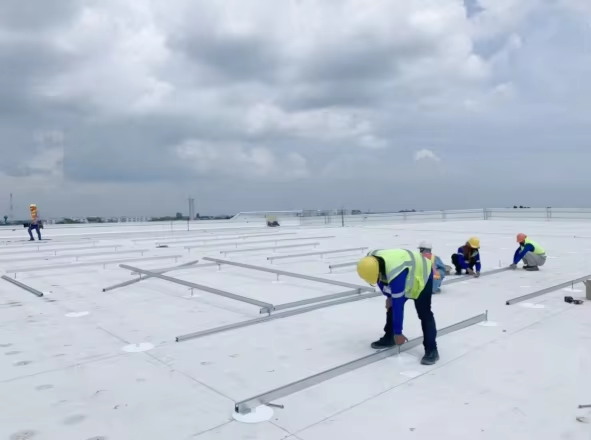
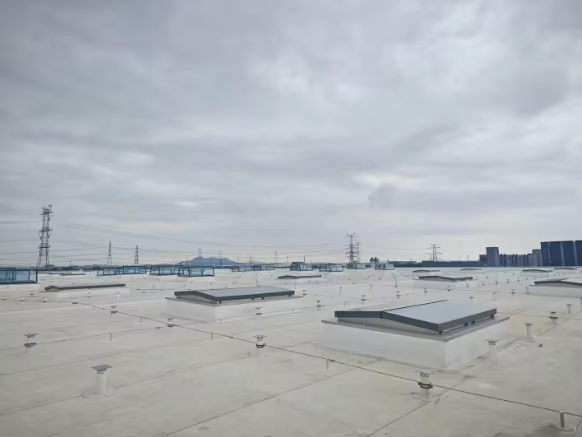
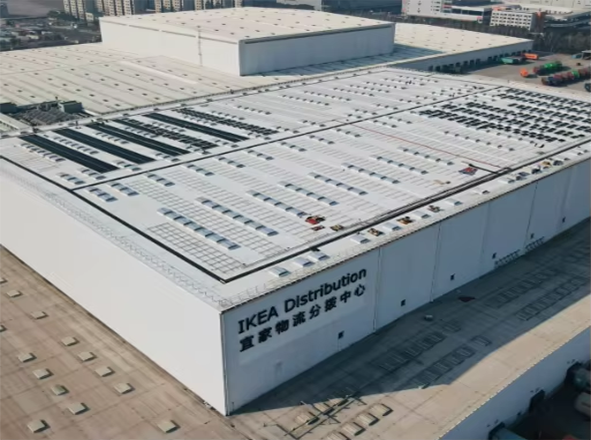
TPO Membrane Installation
Construction points:
1. The thickness of the corrugated steel plate as the base layer should be ≥0.75mm, and it must have a reliable connection with the main structure. The connection of the steel plate should be smooth and continuous, without any sharp protrusions. The concrete base should be flat, dry, and free of defects such as honeycombs and cracks.
2. Pre-laying of TPO rolls: After the rolls are laid and unfolded, they should be placed for 15 to 30 minutes to fully release the internal stress of the rolls and avoid wrinkling during welding.
3. Mechanically fix the lower roll: The fixings should be arranged straight and evenly, and the spacing between the fixings should meet the design requirements. The fixings around the roof and in the corner area should be denser.
4. Hot air welding: The upper roll covers the mechanical fasteners of the lower roll to form an overlap of not less than 120mm. The automatic welding machine is used for uniform welding, and the weld width is not less than 40mm. The contaminated overlap of the roll should be cleaned before welding.
5. Detailed node processing: For details such as corners, pipe roots, and skylights, TPO prefabricated parts or non-reinforced TPO flashing membranes are used as waterproof layers, and hot air welding is used with the main waterproof layer. The end of the vertical TPO membrane is mechanically fixed with a metal double-mouth strip, and finally sealed with a sealant.
Packing And Delivery
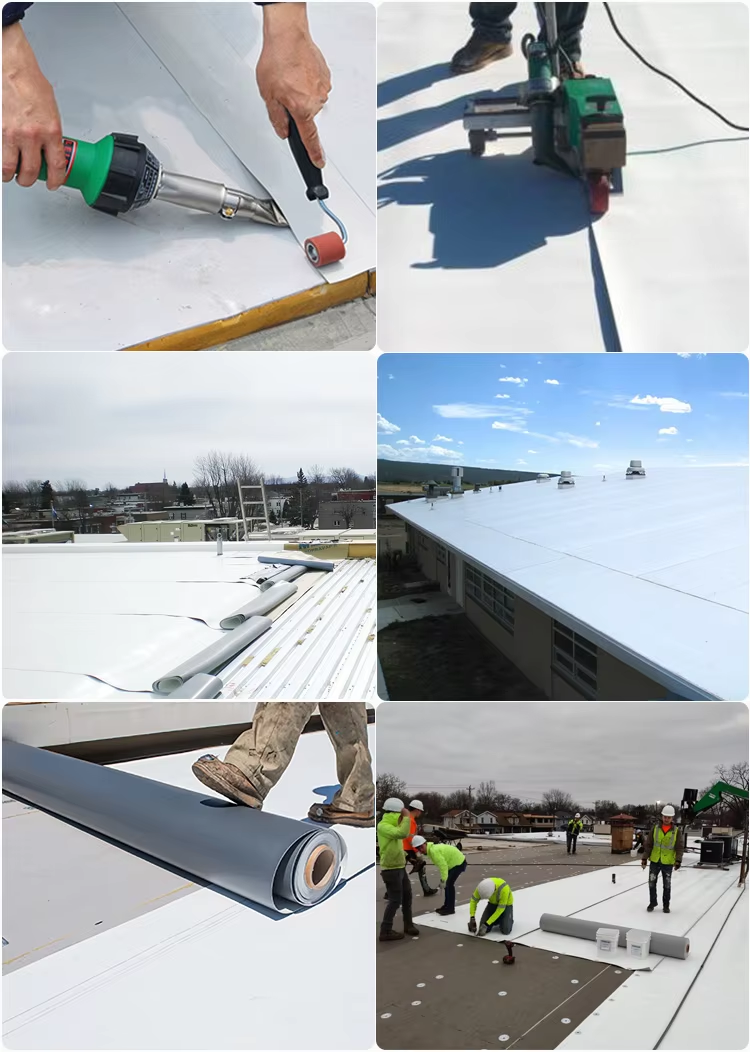
Packed in roll into PP woven bag.
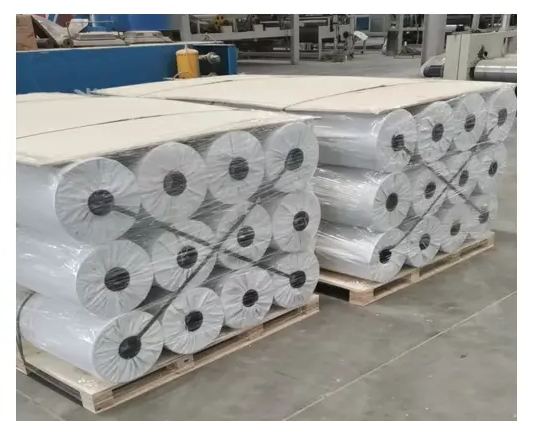
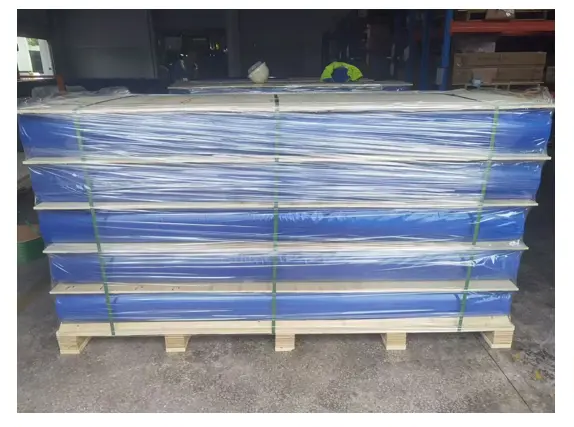
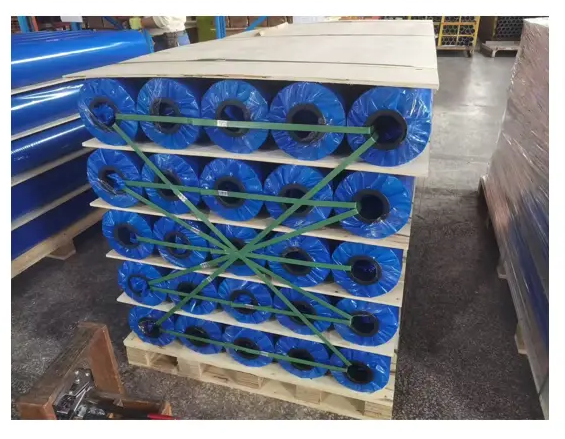
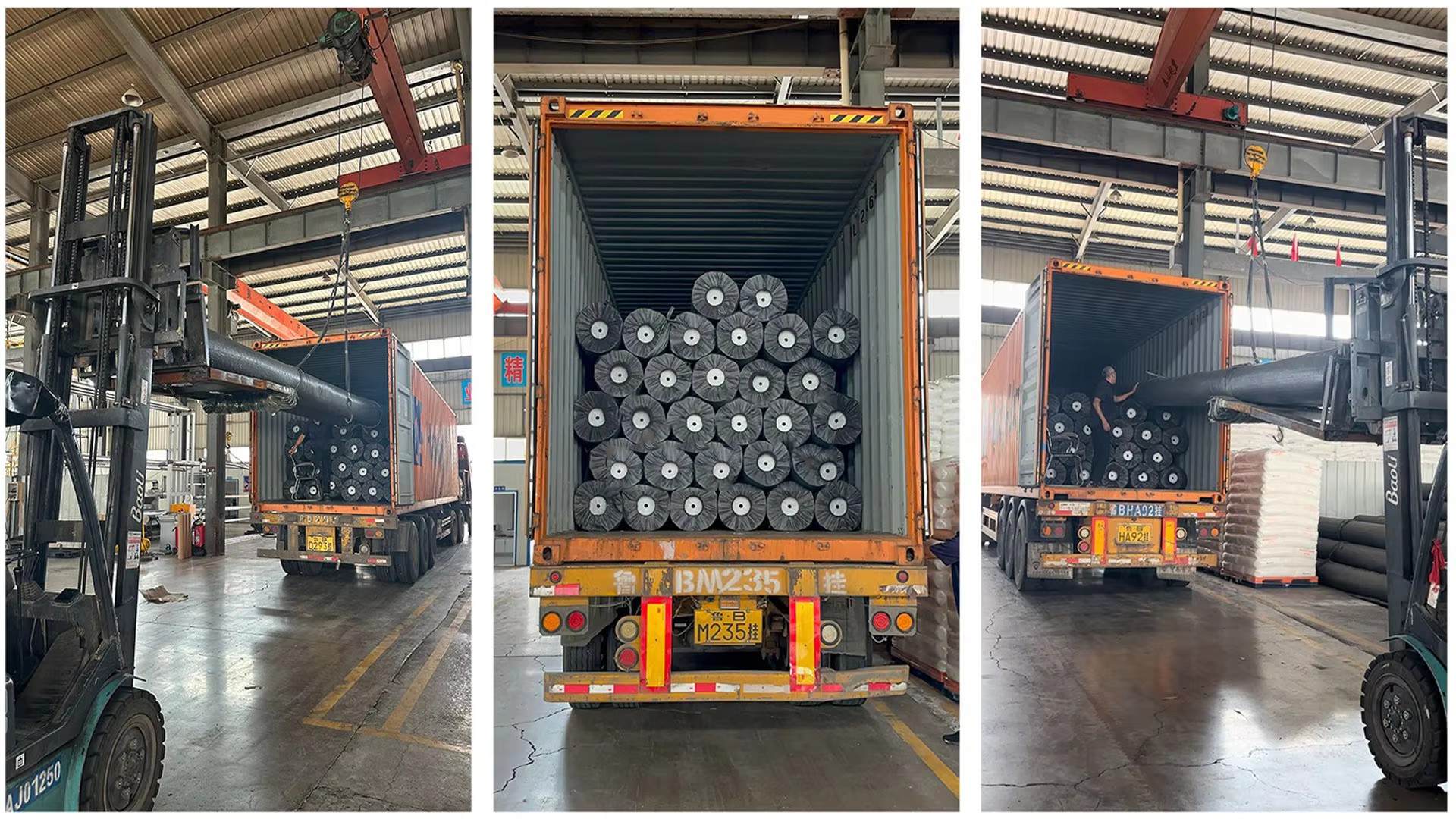