tpo membrane roof
TPO Membrane Introduction
Thermoplastic Polyolefin (TPO) waterproof membrane is a new waterproof membrane made of thermoplastic polyolefin (TPO) synthetic resin that combines ethylene propylene rubber and polypropylene using advanced polymerization technology, and is added with antioxidants, anti-aging agents, and softeners. It can be made into an enhanced waterproof membrane with polyester fiber mesh cloth as internal reinforcement material. It belongs to the category of synthetic polymer waterproof membrane products.
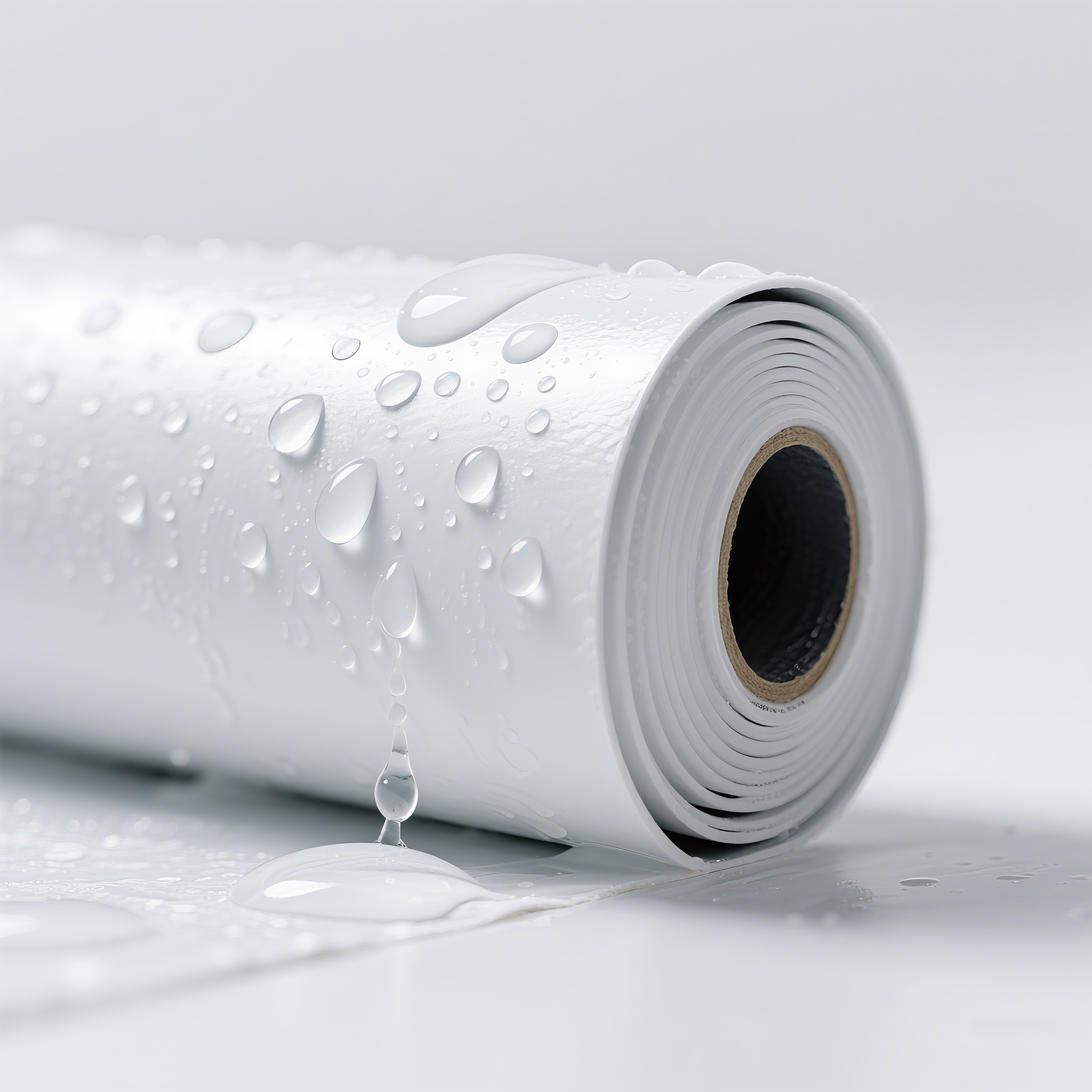
TPO Membrane Specification
Product Name
|
TPO Membrane roof
|
Thickness
|
1.2mm 1.5mm 1.8mm 2.0mm
|
Width
|
2m 2.05m 1m
|
Color
|
White , grey or customized
|
Reinforcement
|
H type, L type ,P type
|
Application Method
|
Hot air welding,Mechanical fixation,Cold sticking method
|
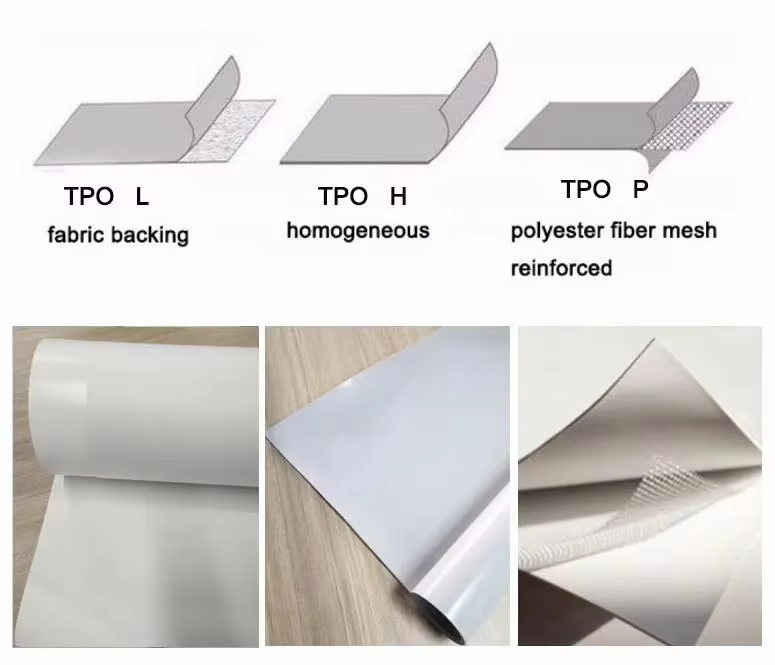
TPO Mrmbarne Standard
No. |
Item |
Standard |
|||
H |
L |
P |
|||
1 |
Thickness of material on the reinforcement/mm ≥ |
- |
- |
0.40 |
|
2 |
Tensile Property |
Max Tension/ (N/cm) ≥ |
- |
200 |
250 |
Tensile Strength/ Mpa ≥ |
12.0 |
- |
- |
||
Elongation Rate/ % ≥ |
- |
- |
15 |
||
Elongation Rate at Breaking/ % ≥ |
500 |
250 |
- |
||
3 |
Heat treatment dimensional change rate |
2.0 |
1.0 |
0.5 |
|
4 |
Flexibility at low temperature |
-40℃, No Cracking |
|||
5 |
Unpermeability |
0.3Mpa, 2h, No permeability |
|||
6 |
Anti-impact property |
0.5kg.m, No seepage |
|||
7 |
Anti-static load |
- |
- |
20kg, No seepage |
|
8 |
Peel Strength at joint /(N/mm) ≥ |
4.0 |
3.0 |
3.0 |
|
9 |
Right-angle tear strength /(N/mm) ≥ |
60 |
- |
- |
|
10 |
Trapeaoidal tear strength /N ≥ |
- |
250 |
450 |
|
11 |
Water absorption rate(70℃, 168h) /% ≤ |
4.0 |
|||
12 |
Thermal ageing (115℃) |
Time/h |
672 |
||
Appearance |
No bundles, cracks,delaminatetion,adhesion or holes |
||||
Performance retention rate/ % ≥ |
90 |
||||
13 |
Chemical Resistance |
Appearance |
No bundles, cracks,delaminatetion,adhesion or holes |
||
Performance retention rate/ % ≥ |
90 |
||||
12 |
Artificial climate accelerates ageing |
Time/h |
1500 |
||
Appearance |
No bundles, cracks,delaminatetion,adhesion or holes |
||||
Performance retention rate/ % ≥ |
90 |
||||
Note: | |||||
1. H type is the Normal TPO membrane | |||||
2. L type is the Normal TPO coated with the non-woven fabrics at the back side | |||||
3. P type is the Normal TPO reinforced with the fabric mesh |
Product Features
1.NO plasticizer and chlorine element. It is friendly to environment and human body.
2.Resistance to high and low temperature .
3.High tensile strength,tear resistance and root puncture resistance .
4.Smooth surface and light color design,energy saving and no pollution.
5.Hot air welding,it can form a reliable seamless waterproof layer.
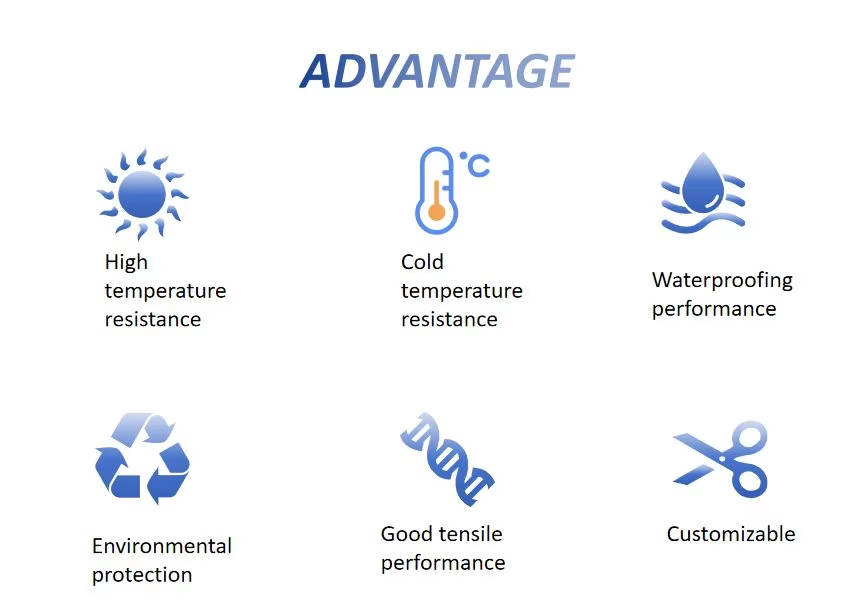
TPO Membrane Application
It is mainly applicable to various roof waterproof systems such as industrial and civil buildings and public buildings.
Tunnel, underground pipe gallery, subway, artificial lake, metal steel roof, planted roof, basement, master roof.
P-enhanced waterproof membrane is applicable to the roof waterproof system of mechanical fixation or empty roof pressing;
L backing waterproof membrane is applicable to the roof waterproof system of basic-level full sticking or empty roof pressing;
H homogeneous waterproof membrane is mainly used as flooding material.
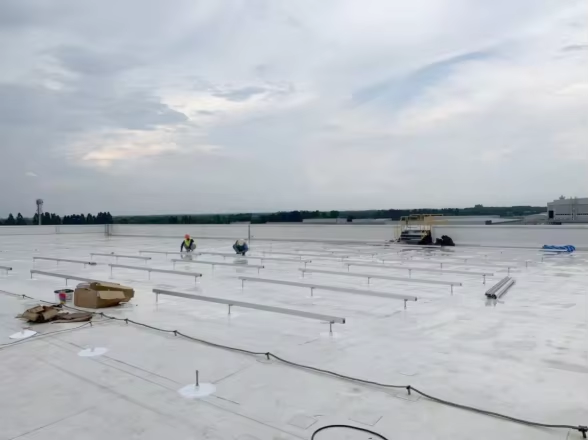
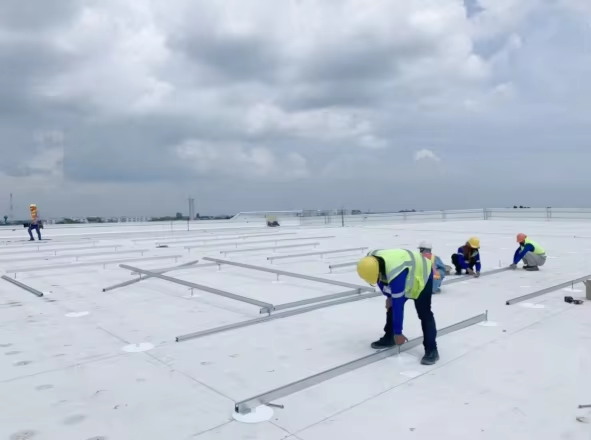
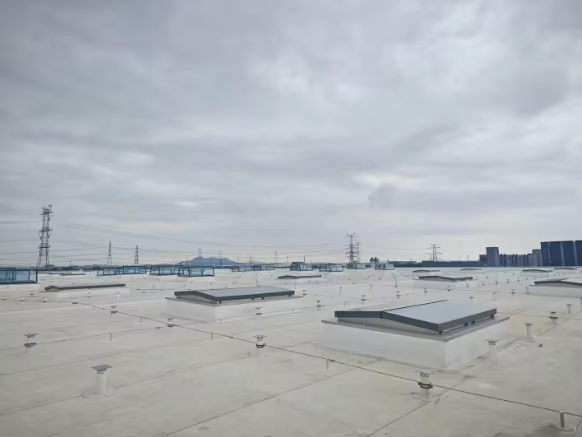
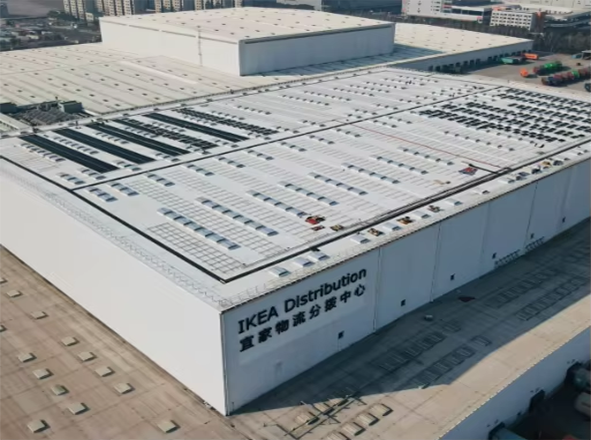
TPO Membrane Installation
TPO fully bonded single-layer roof system
The backing type TPO waterproof membrane is fully bonded to the concrete or cement mortar base, and the adjacent TPO membranes are welded with hot air to form an overall single-layer roof waterproof system.
Construction points:
1. The base layer should be dry, flat, and free of floating dust, and the bonding surface of the membrane should be dry, clean and pollution-free.
2. The base adhesive should be stirred evenly before use, and the glue should be evenly applied on both the base layer and the bonding surface of the membrane. The glue application must be continuous and uniform to avoid leakage and accumulation. It is strictly forbidden to apply the glue to the overlap welding part of the membrane.
3. Leave it in the air for 5 to 10 minutes to dry the adhesive layer until it is not sticky to the touch, roll the roll to the glue-coated base and bond it with a special roller to ensure a firm bond.
4. Two adjacent rolls form an 80mm overlap, hot air welding is used, and the welding width is not less than 2cm.
5. The surrounding area of the roof should be fixed with metal strips.
Packing And Delivery
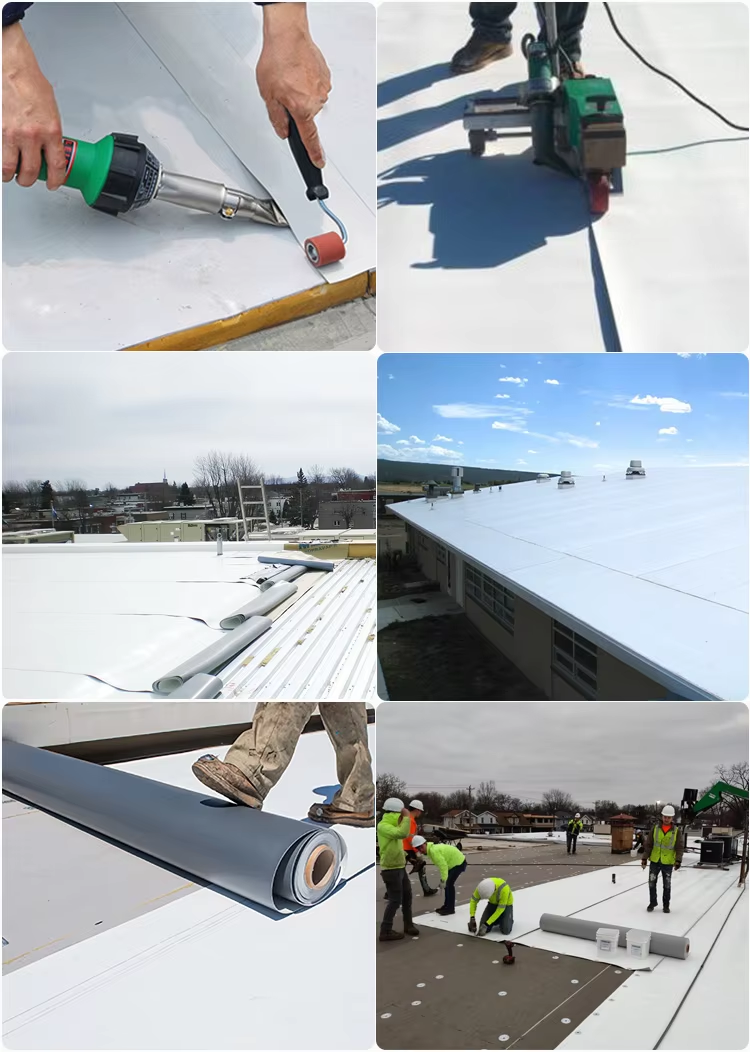
Packed in roll into PP woven bag.
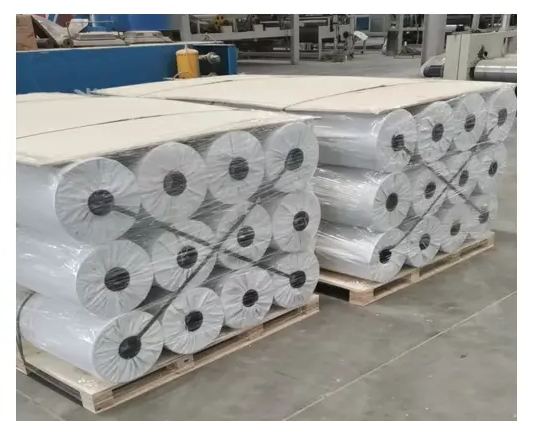
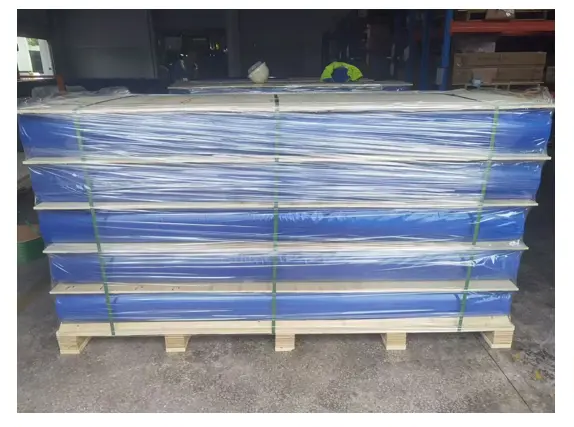
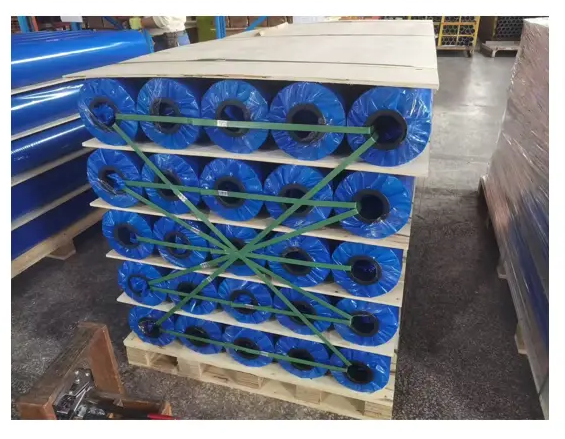
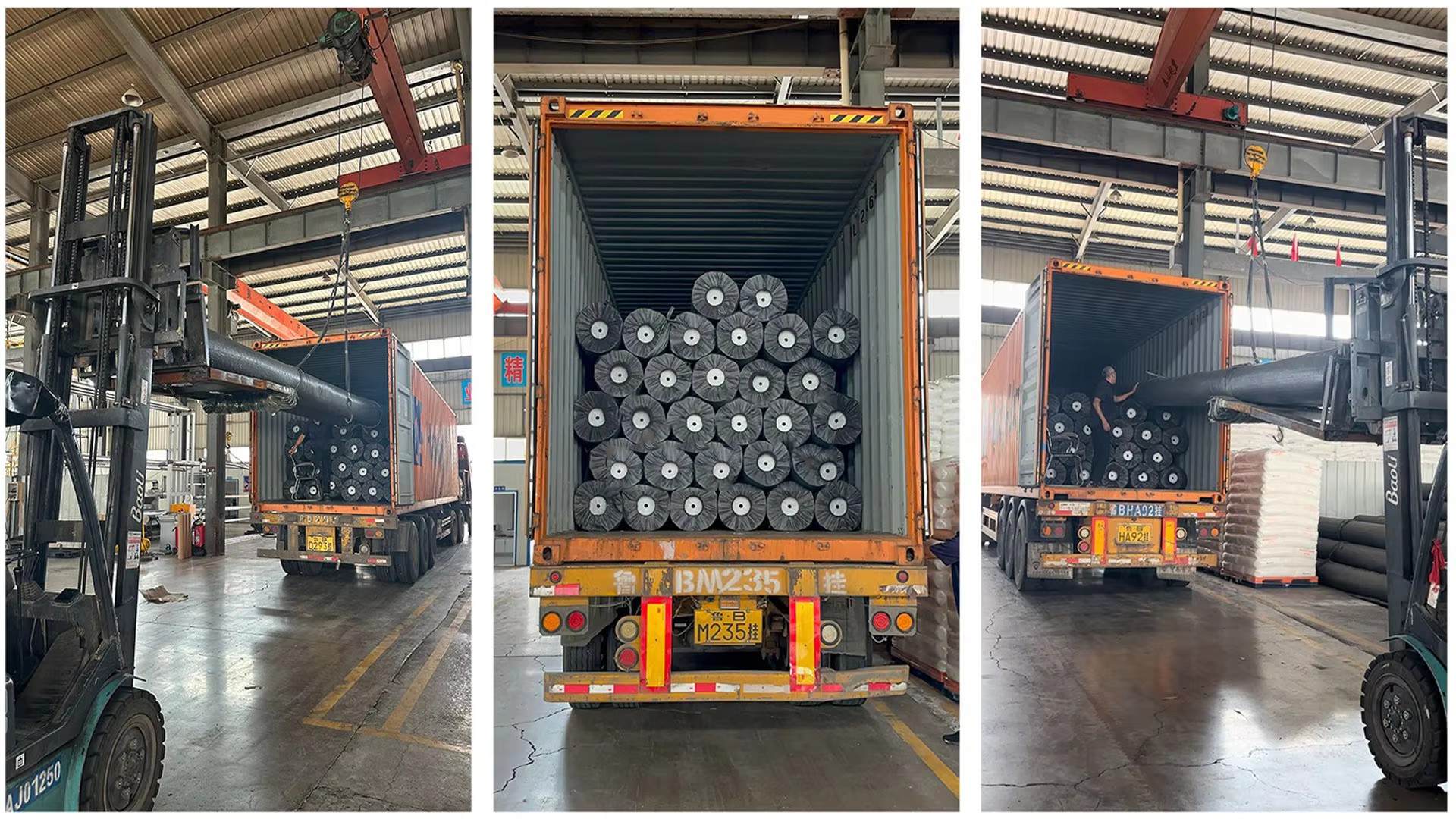